Blogs
Resources and insights
Blogs
Resources and insights
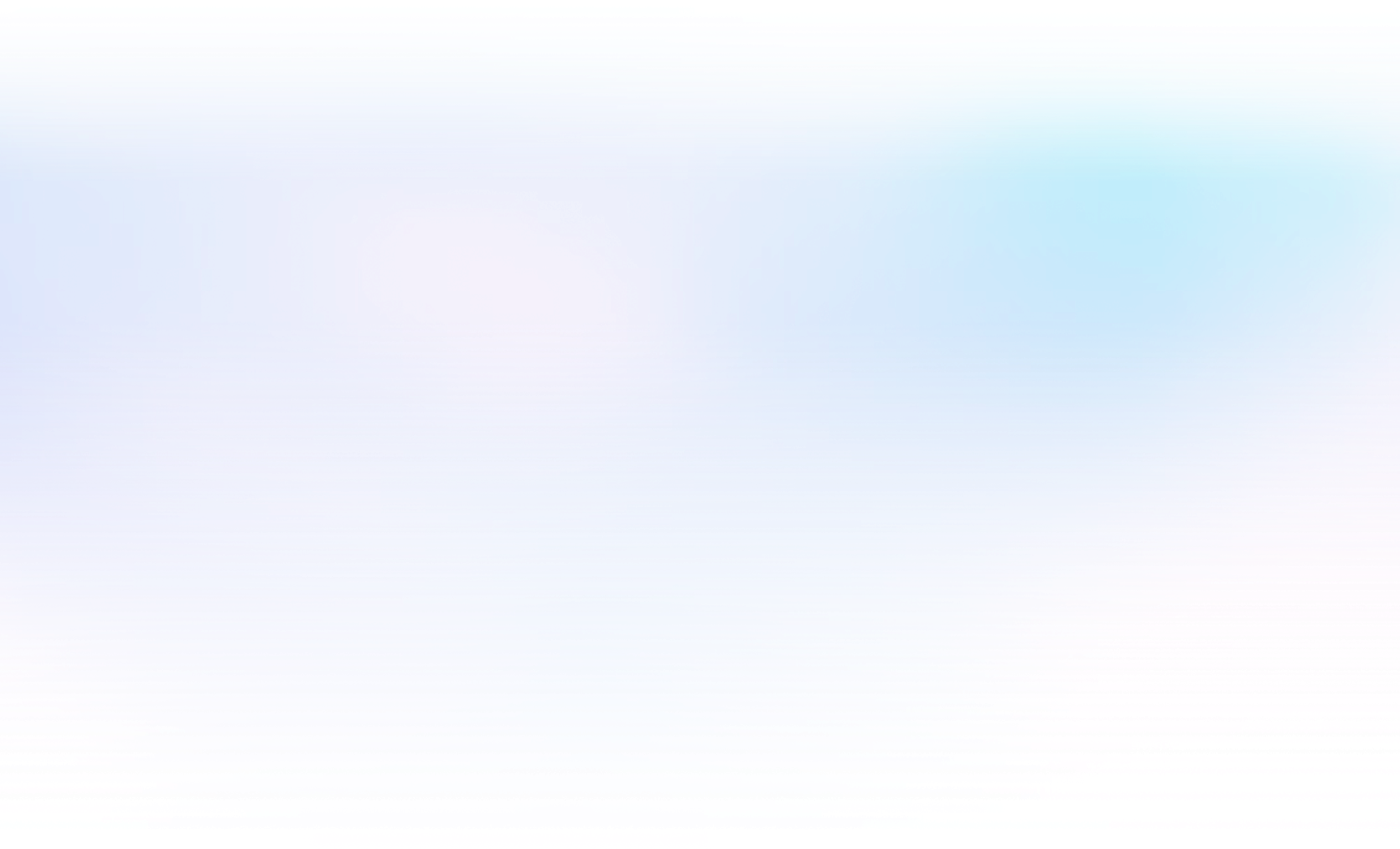
Joint Stock Company Elmoris Ltd. is a modern and rapidly expanding company which produce “Twist-off“ style caps in various sizes, lacquered and printed according to clients’ design and specification.
Their goal is to understand and satisfy their clients’ needs. This has allowed them to become the market leader in the Baltic States. Elmoris also has a very strong presence in The Netherlands, Poland, Slovakia, Russia, Ukraine, Azerbaijan, Kazakhstan etc. In early 2006 Elmoris expanded the manufacturing facilities to a new site in Belarus. Today, in 2015, Elmoris sells to 32 countries worldwide, including the United Arab Emirates and New Zealand, with merely about 10% of the output staying in the Baltic States.
Due to nature of the purchasing and production process the costs in Elmoris varies significantly: - different purchasing costs, - different landed costs, - different metal sheets thickness, - surface properties, - quality problems, - and other variances, are causing constant changes of the purchasing costs, coating/painting recipes and production yield.
Cases exists when the Customers supply their own metal sheets, so the cost of metal sheet for Elmoris is zero - and yet the finished products are more costly due to bad metal sheets quality which causes both material and machine time waste. Elmoris needs to be able to pinpoint and prove such cases to Customer.
Elmoris used a planned costing method before. To get some approximation of the actual costs of materials and products they had to spend a lot of time with their numbers. Unassigned cost variances were simply unmanageable.
All these facts demanded an implementation of a costing method which calculates the exact cost of materials and products.
In 2011 they heard about ACM and invited us to implement it ASAP. It was during the European Basketball Championship in Lithuania, so we had fun all days - with ACM until evenings, and with basketball on evenings!
Today ELMORIS uses full ACM functionality. Now they have a total control over costs and not single variance remains unassigned. All variance accounts are now obsolete. They know the exact yield for every lot, and exact profit for every shipment position, not only by item number but also by lot number.
They post the costing results monthly to GL and get the exact picture of their business results without any additional work. Reporting to the bank is now credible and demands no additional effort.
Mrs. Galina Ceresko, the CFO in ELMORIS, confirms the results: “With ACM we are able to establish the total and exact control over costs of material and products. No cost variances exist and there is no doubt about profit or loss on each product or semi product. We spend almost no time with preparing the management and bank reports.”
Blogs
Blogs