.png)
Three Different Solutions for Marking and Tracing are Available
- Eagle Europe RF Express for QAD Enterprise Applications
- QAD Automation Solution
- M2M bar code customized solutions
Eagle Europe RF Express for QAD Enterprise Applications
Eagle provides electronic data capture solutions for companies using QAD Enterprise Applications. Eagle are QAD’s Alliance Product Partner for data collection with the class leading product RF Express for QAD Enterprise Applications.
The solution, available from MFG/PRO 7.3k to the latest QAD EA2016 is used in over 1000 sites across the globe and is the only fully integrated electronic data capture solution for QAD Enterprise Applications. This gives a ready to deploy but fully configurable solution, for your data capture, bar coding, RFID and labelling needs. The solution is specialised on working with companies in the automotive, consumer products, high-tech, food & beverage, industrial products and life-science markets.
Software
RF Express for QAD Enterprise Applications addresses the many business problems associated with Data Collection such as laborious manual systems, excessive paper forms, inaccurate and invalidated collections and delayed data posting.
RF Express for QAD Enterprise Applications is a 100% on-line, realtime automated data collection solution. RF Express™ optimizes the QAD Enterprise Applications enterprise solution, adding new functionality, enhanced processing speed and the ability to integrate distributed operations. Because of its flexible architecture, RF Express™ for QAD Enterprise Applications adapts easily to changes in business processes. In addition, Eagle’s Progress-based product offers “plug and go” integration with QAD Enterprise Applications and makes the most of a robust family of data collection devices.
RF Express for QAD Enterprise Applications provides the user with a streamlined interface for the corresponding QAD Enterprise Applications transaction. The user sees, and responds to, one question at a time, and each response is validated instantaneously within the QAD Enterprise Applications database, thereby giving immediate warnings of incorrect physical transactions. As a user proceeds through a transaction, the actual lower level routines within QAD Enterprise Applications are executed. Typical uses include:
Paperless RF terminal receiving with integrated label printing
- Paperless material requisitioning, RF terminal material movement and put away
- Paperless RF terminal cycle counting and physical inventory
- Shop floor labour collection
- Finished goods warehousing and shipping
With its high degree of scalability, RF Express™ for QAD Enterprise Applications can be quickly installed at one site and then rolled out to numerous additional facilities as needed. Its flexible architecture makes it easily adaptable to changes in business processes or requirements.
Product Strengths
- QAD partner of the year on multiple occasions (most recently 2014)
- “Plug and go” integration with QAD Enterprise Applications (7.3K to the latest QAD EA 200x release)
- 100% Online Validation
- Comprehensive solution – Over 100 Standard Transactions
- Over 1000 Worldwide Customers
- Dynamic / evolving product
- Robust family of automated data collection devices
- Sound technology base.Real-time, streamlined input to the QAD Enterprise Applications database
- Input with QAD Enterprise Applications edits and logic
- Increased data visibility with reduced data entry input
- Integrated label generation and bar code scanning
QAD Automation Solutions
QAD Automation Solutions improves manufacturers’ material transactional effectiveness and efficiency by aligning QAD Enterprise Applications and QAD Cloud ERP with material processes. There are two primary components to the solution:
- Data Collection captures material and production data through simplified ERP transactions using a mobile device such as a radio frequency (RF) scanner, tablet or a stationary shop floor personal computer or terminal.
- Label Printing Services routes and prints labels associated with material and production transactions according to manufacturer, supplier and customer specified formats and rules. These capabilities help manufacturers better align their material logistics processes in a timely fashion while ensuring inventory accuracy through process compliance.
Value and Benefits
The main value received from Automation Solutions is improved operational visibility, control and accuracy throughout the internal supply chain, from inbound through production to outbound. Specific benefits include:
Increases visibility and control - through dynamic task generation. Electronically ensures all workers focus on the right priorities, replacing printed task dispatch and pick lists that often become stale, are lost or are difficult to manage.
Reduces costly errors - through real-time validation. The solution automatically notifies users when they are about to make a mistake, preventing errors such as receiving invalid items or quantities, transferring materials to invalid locations, picking or issuing incorrect lots for a work order or when attempting to load a truck with the wrong pallet.
Streamlines inbound processes – leveraging ERP inbound receiving packaging. Scan pallets and boxes into stock while verifying the supplier ASN. Using tailored put-away logic, the user is automatically directed to the put-away location including crossdocking, production line or warehouse zone.
Streamlines production replenishment – with bulk picking transactions. Users electronically pick and replenish work center/line locations per multi-order helping to meet the demand for components based on real-time schedule priorities.
Improves accuracy and control over production order pick/issue process – where discrete order component kitting is required. Users pick components and associate them to a container where downstream transactions such as inventory transfers and material issue to work order can occur, with a single scan of the work order “Kit” container.
Reduces costly mislabeling – using configuration based rules to print the correct customer label based on any system data, such as site, item, customer and location. This ensures the printing of the correct label at the desired time.
Increases label printing efficiency – through systemdata driven selection of label format and printing device. Print labels at the appropriate steps in the process, using the correct label format, using the correct printer(s).
Minimizes data errors and redundancy – by being a native component of the QAD Enterprise Applications or QAD Cloud ERP solution. In addition to native ERP support, label printing tightly integrates with the Data Collection component, Serialization and QAD Enterprise Asset Management.
Compliance Ready – through certified and auditable instant monitoring capabilities that provide the status of when, where and by whom labels were printed for a given site, customer, ship-to or item.
Easy Label Printing Exception Handling – enables copying of existing labels, altering them and printing instantly.
Full control of your labels – by providing a simple yet effective in-house label printing service, reducing dependence on external service providers.
M2M Bar Code Customized Solutions
M2M bar code customized solution is the best choice when a company plans to cover relatively small number of business transactions with marking and tracing - using bar code, QR, or RFID.
The approach is to analyze the requirements of the company, model the solution, and customize the selected transactions in a way they produce bar code (or QR, or RFID) labels, capture data through scanning, and load them to the core ERP.
M2M bar code customized solutions is a cost efective solution - in case that limited number of transactions must be customized.
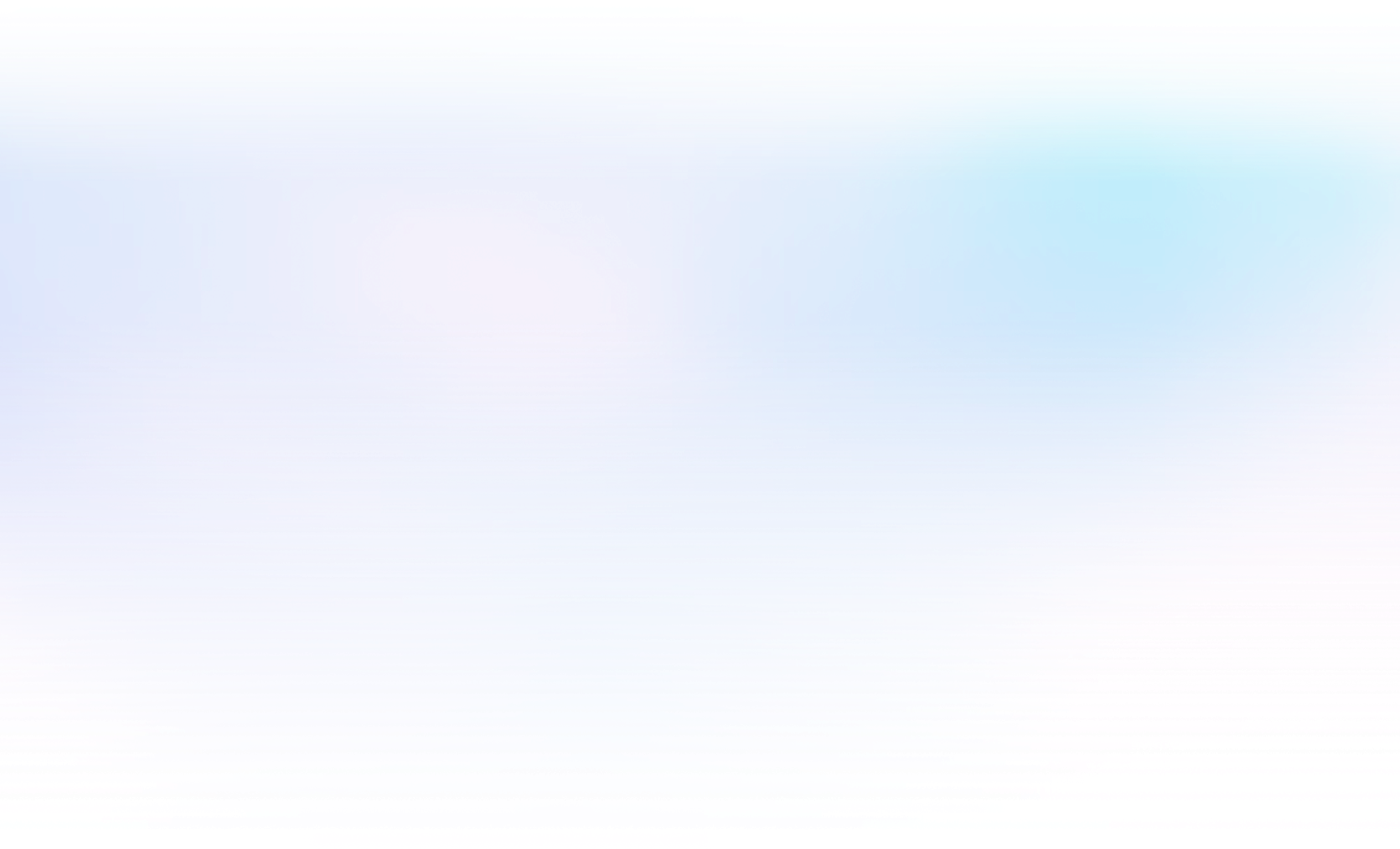
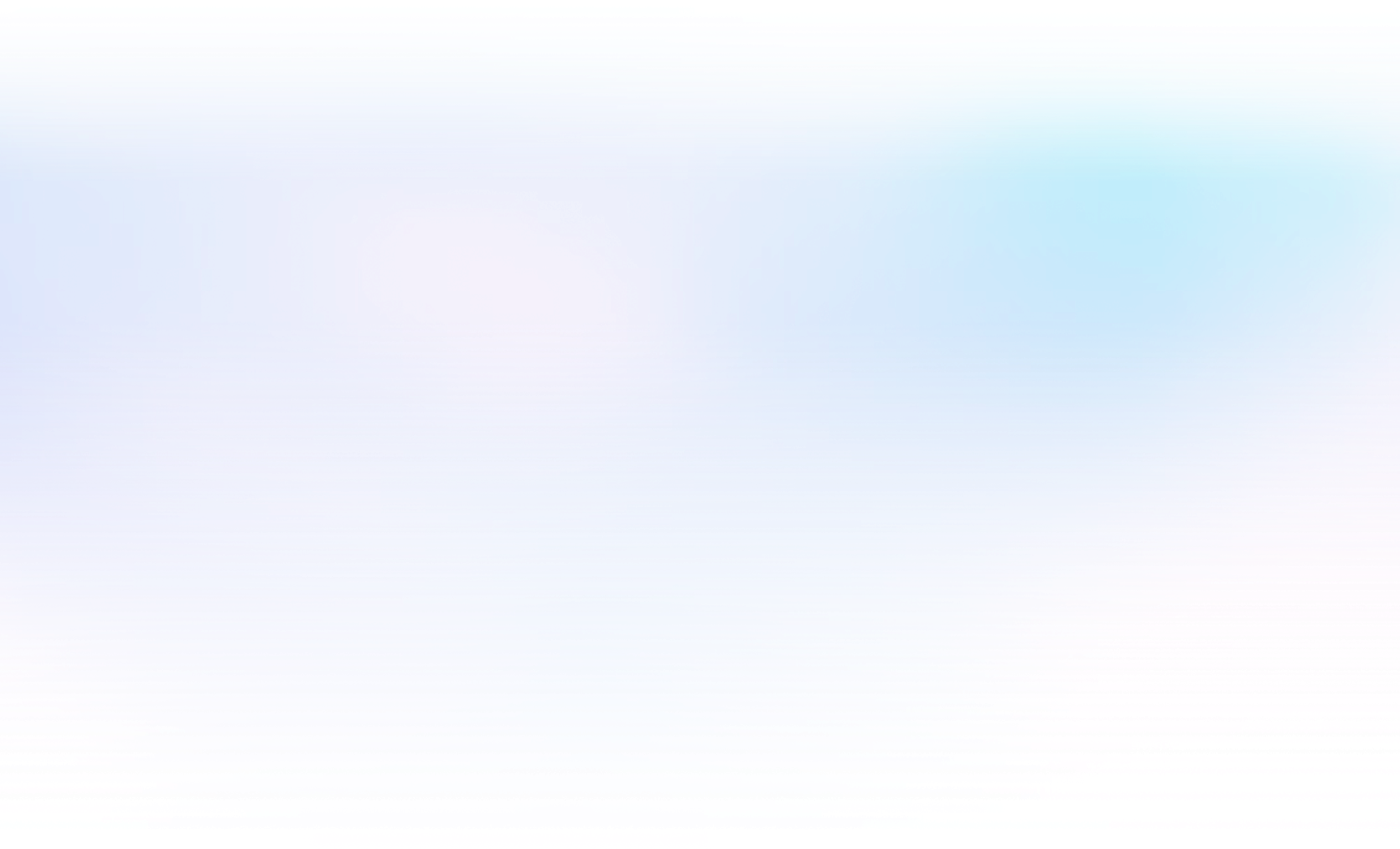